An example of research results
Lubrication under extreme temperatures can significantly affect the performance and life of the reducer due to changes in the temperature distribution in the reducer complicated by internal heat generated by sliding and heat flow in and out of the reducer. We have developed the prototype speed reducer shown in Figure 1 by optimizing the lubrication design to match these thermal changes and individual sliding configurations.
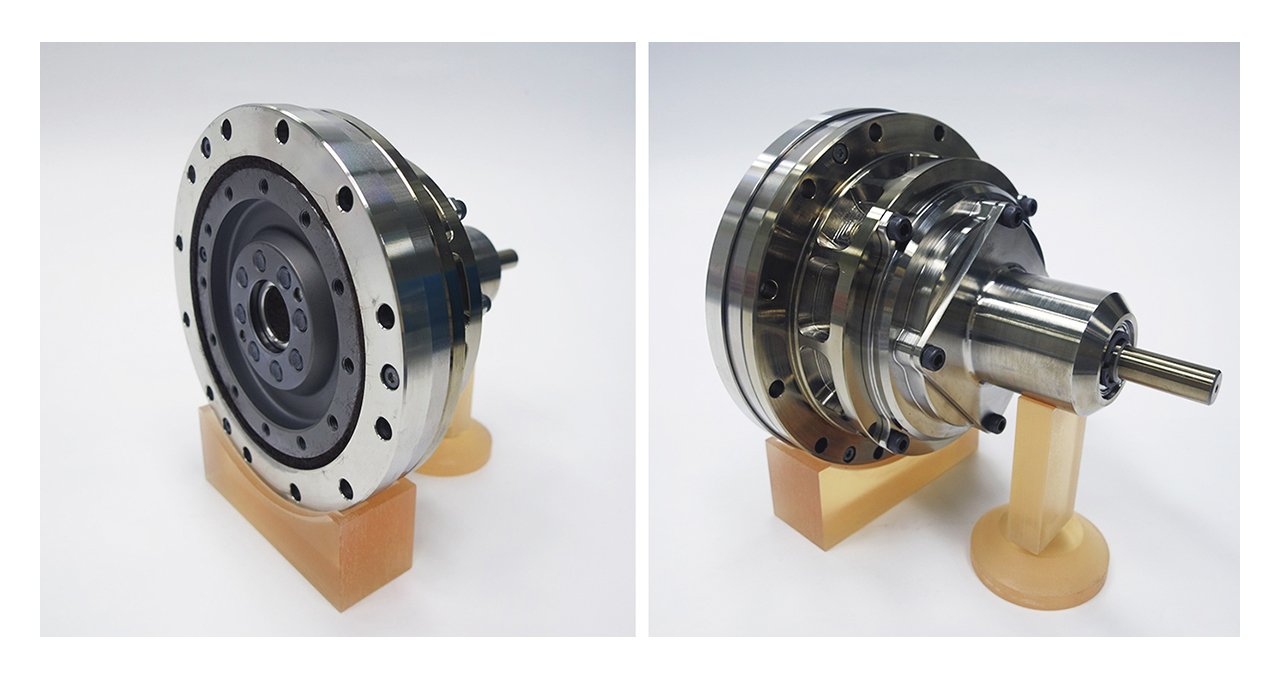
The test equipment also had developmental elements and was designed and fabricated with consideration of thermal effects so that the performance of the reducer could be evaluated. Figure 2 shows the test apparatus, and Figure 3 shows the inside of the vacuum chamber. Currently, a vacuum chamber is used to simulate the space environment. The performance and operating life of the reducer are being evaluated in a vacuum and at extreme temperatures (-200°C or lower).
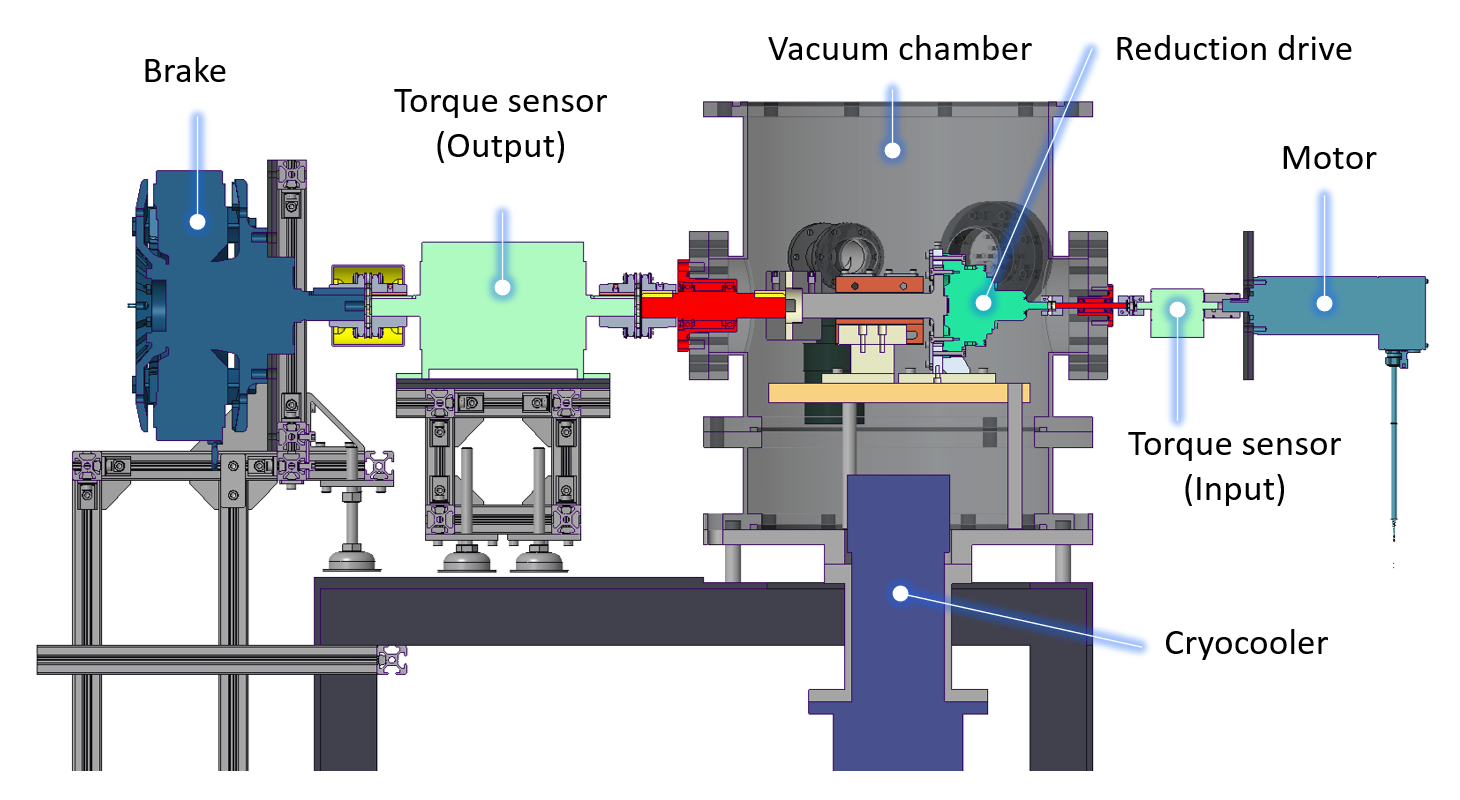
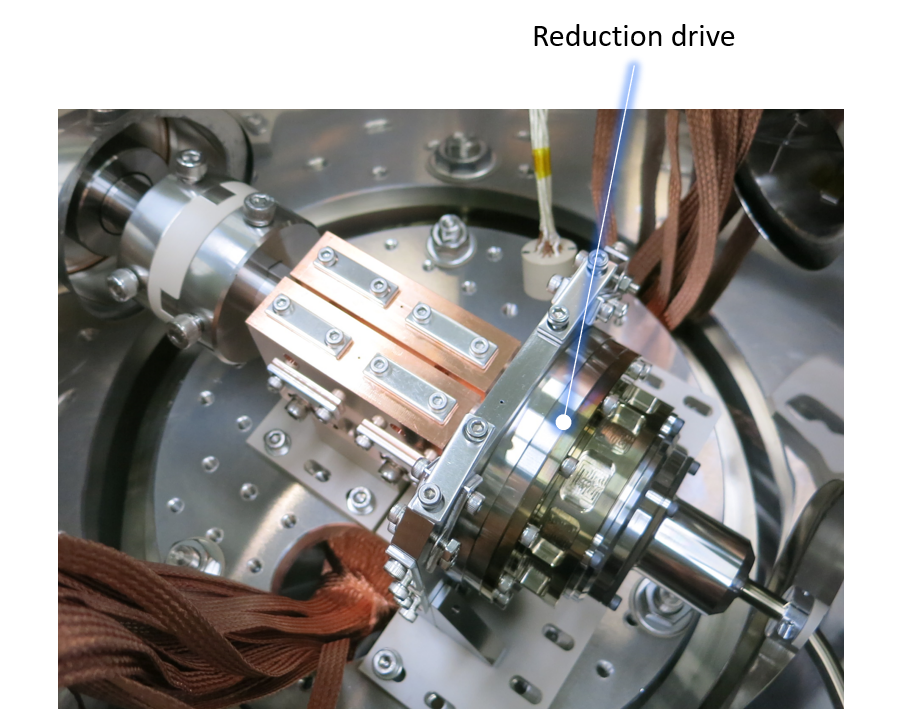