An example of research results
Study of gearboxes with large amounts of oil
As shown in Figure 2, the drive system of a manned pressurized rover is designed to transmit the motor's driving force to the wheels at high torque and low speed through a transmission. The transmission is composed of multiple gears, but the gear tooth surfaces, which transmit power over a small area, are subject to wear and must be properly lubricated.
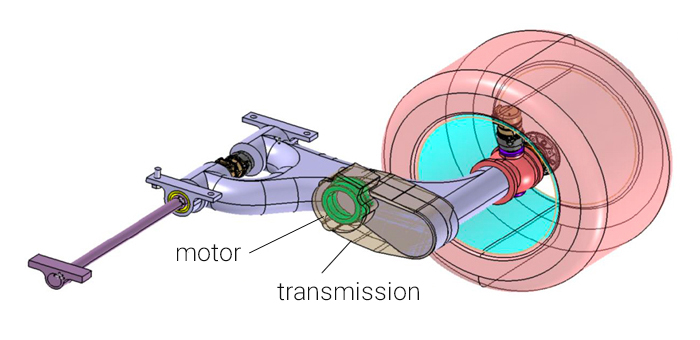
Until now, the sliding parts of spacecraft mechanisms have been lubricated with a small amount of low-vapor pressure oil or a solid lubrication film, but the operating conditions of this drive system are unprecedentedly harsh, and we plan to adopt a completely new lubrication system for spacecraft. Specifically, the plan is to adopt a method of forcibly cooling and lubricating the transmission by injecting a large amount of lubricating oil containing additives to add wear resistance into the transmission and circulate.
If this method can be realized, we will have a lubrication technology that can handle larger, faster spacecraft. We are currently evaluating oil evaporation and sliding characteristics in the lunar environment and researching mechanical parts such as gears, oil pumps, and oil seals.
Research on roller bearings and plain bearings for high load around axles
No other rover in the world has been equipped with a pressurized chamber that allows the crew to travel without space suits. As a result, the rover will be larger, and the bearings that support the body load will be subjected to higher loads than in the previous spacecraft. The load-bearing body must withstand long-distance travel under high loads, and research is underway to establish a lubrication technology for the bearings.