Outline of the Research
This research aims to improve the reliability of attitude control components such as space flywheels and gyros. We are accumulating reliability and lifetime data and establishing evaluation methods through long-term continuous operational tests.
The results of this research will contribute to the health evaluation methods, and criteria for attitude control components on the ground and in orbit and will be used to further improve the reliability of attitude control components through the evaluation of test data, planning and evaluation of improvement measures, and reflection in design and processes.
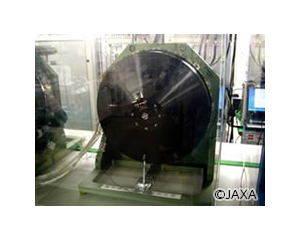
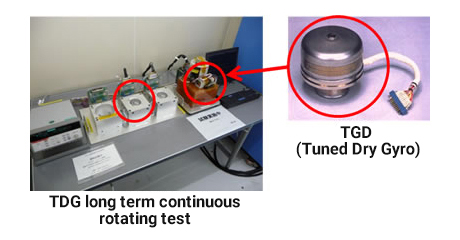
Life Prediction and Acceleration Test Methods for Rolling Bearings
As the lifespan of satellites increases, it becomes increasingly difficult to conduct real-time tests on the life of rolling bearings. Therefore, we are researching life prediction methods and accelerated testing methods that can guarantee a life of 20 years within three years.
One factor that makes life prediction and construction of accelerated tests difficult is that the torque of rolling bearings is nearly constant during the operation and increases sharply just before the end of life. With this kind of transition, it is not clear what happens, at what time, and to what degree while the operation continues toward the end of life. Also, the condition of the bearing cannot be determined, and life prediction is impossible. Therefore, it is important to identify parameters that monotonically increase or decrease during the operating period of a rolling bearing.
Currently, we are studying methods to measure how parameters, such as lubricant viscosity and oil volume, change during the life of a rolling bearing. After the measurement method is determined, we will select parameters suitable for use in the life prediction method, select accelerated test conditions that follow the same degradation process as that of an actual ball on the bearing track, and develop a test method to determine the life of rolling bearings in a short time.
Longer life, larger size, and higher speed bearings
The design life of satellites tends to be extended, and we aim to realize bearings that can be driven continuously for more than 20 years with no maintenance. In this research, we devised a structure that supplies a small amount of lubricating oil to the bearing by utilizing surface tension and completed a long-life bearing unit.
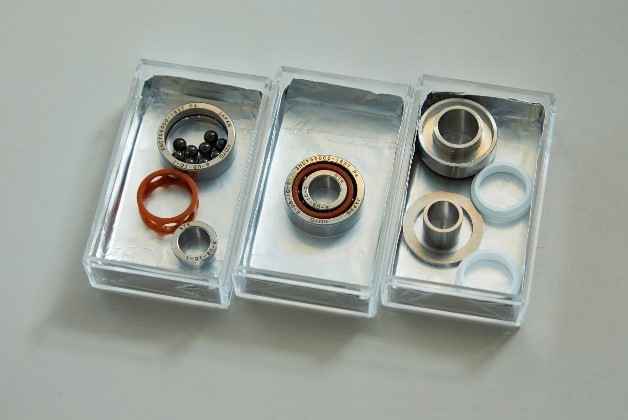
Left side case: outer ring, ceramic balls, cage, and inner ring
Right side case: Porous material (white, photo: polyethylene) and interlacing